thyssenkrupp nucera and Fraunhofer IKTS open First SOEC Pilot Production Plant for Stacks for the Production of Green Hydrogen
thyssenkrupp nucera and Fraunhofer IKTS opened the first SOEC pilot production plant for electrolysis stacks on May 27 in Arnstadt, Thuringia, in the presence of high-ranking representatives from science, politics, and industry. The event was also attended by the Minister President of the State of Thuringia, Prof. Dr. Mario Voigt. With the commissioning of the pilot production plant, the strategic partnership between Fraunhofer IKTS and thyssenkrupp nucera for the development of high-temperature electrolysis (SOEC) is entering the next phase as planned.
In March 2024, the research institute and the world’s leading supplier of highly efficient electrolysis technology for the production of green hydrogen in Arnstadt signed a strategic cooperation agreement for the development of the next-generation SOEC electrolyzer. Building on the development work carried out by Fraunhofer IKTS, thyssenkrupp nucera will now work with Fraunhofer IKTS to advance SOEC technology for the manufacture of stacks for the production of green hydrogen on an industrial scale. With high-temperature electrolysis, thyssenkrupp nucera is strengthening its hydrogen technology portfolio for industrial applications.
The electrolysis stacks are manufactured in the pilot production plant designed and built by Fraunhofer IKTS. The SOEC pilot plant initially produces stacks in small quantities and has a target production capacity of 8 megawatts per year. These stacks are the heart of the future SOEC electrolyzers from thyssenkrupp nucera.
SOEC stack technology is based on an oxygen-conducting ceramic electrolyte substrate with two electrodes, which are assembled together with coupling elements, the chromium-iron (CF) interconnectors, on several layers to form the stack. CF-based SOEC technology guarantees high corrosion resistance, optimized thermal cycle performance, and high long-term stability with regard to temperature cycling. In addition, stack technology requires only a small number of components and occupies a leading position compared to designs currently available on the global market. The SOEC cell design is also well suited for the desired highly automated series production. Thanks to the large-scale industrial and highly automated series production planned for the future, the high-temperature electrolyzer can also be manufactured at competitive costs.
With innovative high-temperature electrolysis, companies will be able to produce green hydrogen highly efficiently in the future. SOEC electrolysis ensures high efficiency because less electrical energy is required to split water vapor at high temperatures. When commercial high-temperature electrolysis is used in processes that generate large amounts of waste heat, such as in the steel industry, electricity consumption can be reduced by 20% to 30% compared to other technologies.
In addition, SOEC technology offers the major advantage of utilizing industrial CO2 as a raw material and converting it into green synthesis gas together with green hydrogen. This in turn can be used to produce sustainable chemical feedstocks and e-fuels—a unique selling point with enormous potential for the energy transition.
“The outstanding properties of SOEC technology have prompted us to work with our strategic partner Fraunhofer IKTS to develop high-temperature electrolysis to market maturity. We are convinced of the advantages of this electrolysis technology for the production of green hydrogen. It will play a central role in a new, climate-friendly energy mix,” says Dr. Werner Ponikwar, CEO of thyssenkrupp nucera.
“By integrating SOEC technology into industrial waste heat sources or directly generating synthesis gas from water and CO2, companies can maximize the efficiency of green hydrogen production and effectively implement their decarbonization strategy. These unique advantages make SOEC technology a real game changer,” says Professor Alexander Michaelis, Director of Fraunhofer IKTS.
The operation of the pilot production plant will generate the necessary experience that will be incorporated into the construction of a fully automated, large-scale industrial SOEC production plant for high-performance stacks.
Other news from the department research and development
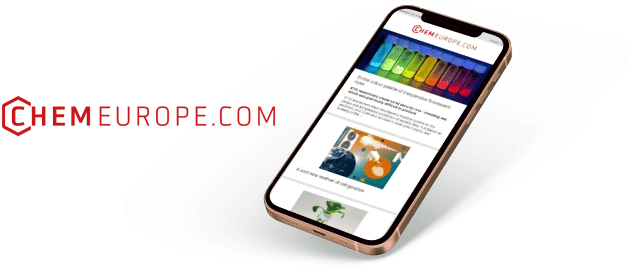
Get the chemical industry in your inbox
By submitting this form you agree that LUMITOS AG will send you the newsletter(s) selected above by email. Your data will not be passed on to third parties. Your data will be stored and processed in accordance with our data protection regulations. LUMITOS may contact you by email for the purpose of advertising or market and opinion surveys. You can revoke your consent at any time without giving reasons to LUMITOS AG, Ernst-Augustin-Str. 2, 12489 Berlin, Germany or by e-mail at revoke@lumitos.com with effect for the future. In addition, each email contains a link to unsubscribe from the corresponding newsletter.
Most read news
More news from our other portals
Last viewed contents
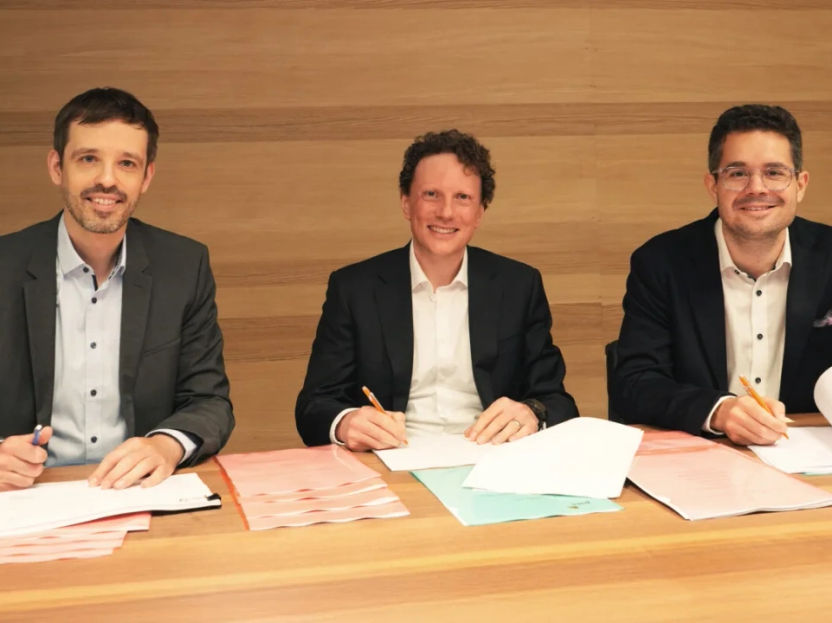
Largest carbon removal investment round globally year to date - Climeworks raises USD 162M to scale up technology
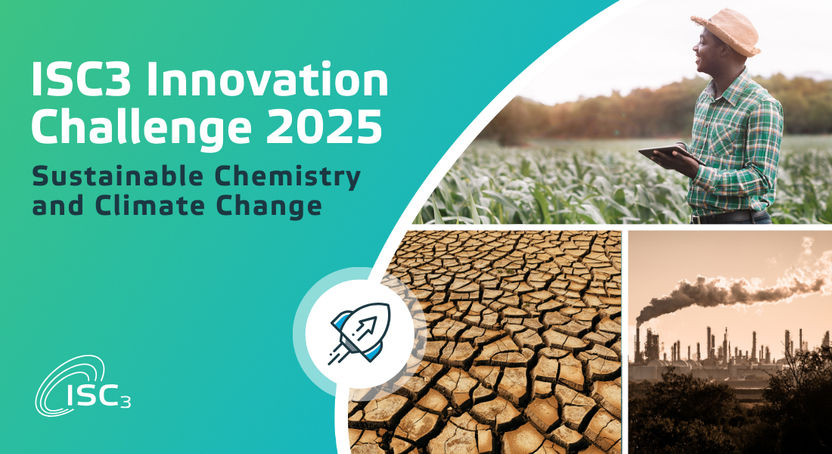
Finalists Announced for the ISC3 Innovation Challenge 2025 on “Sustainable Chemistry & Climate Change” - Ready, set, here are the Changemakers!
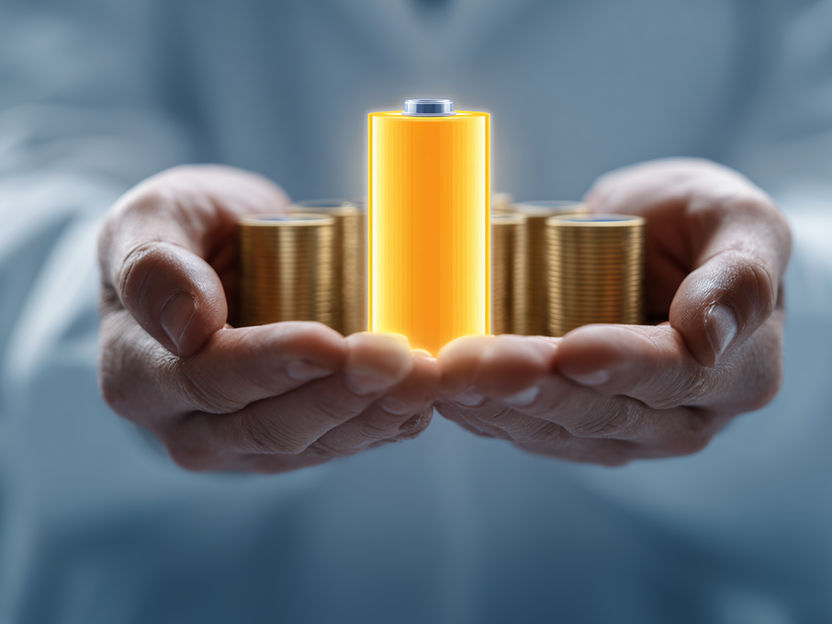
CustomCells secures its future with new investors - New investors secure development and production of state-of-the-art battery cells at the technology cluster in Itzehoe
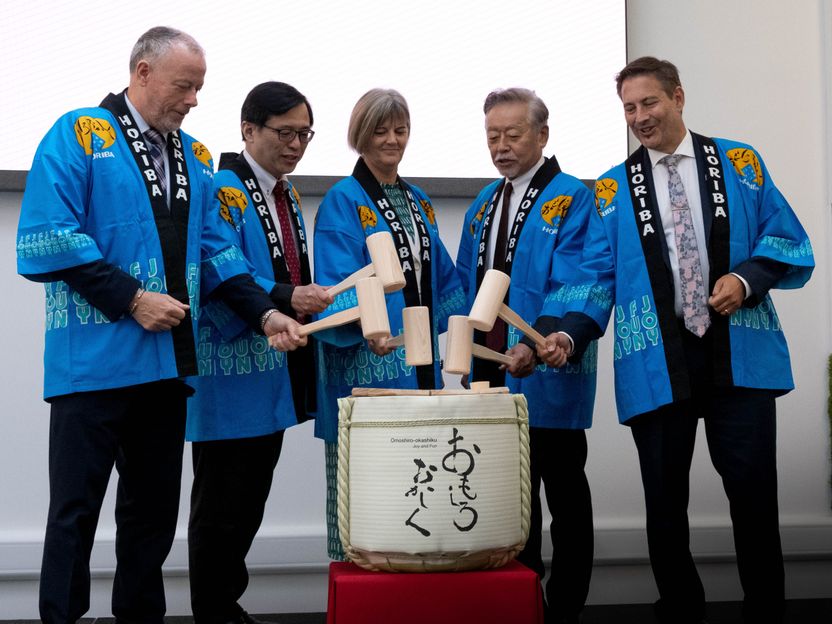
HORIBA opens new Analytical Solution Plaza to support UK science and research
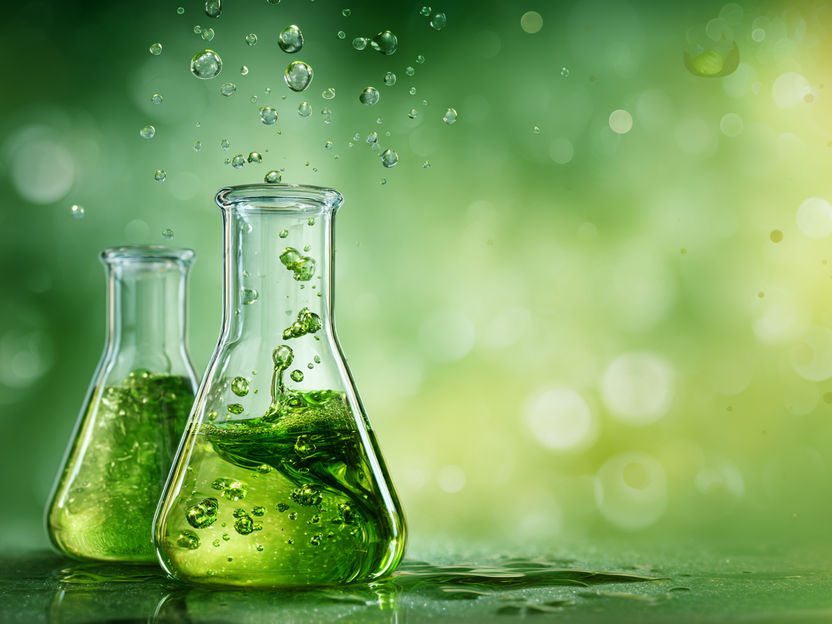
Check the sustainability of chemicals easily onlin - Freely available web application helps users of chemicals, including product manufacturers, to assess the sustainability of their products
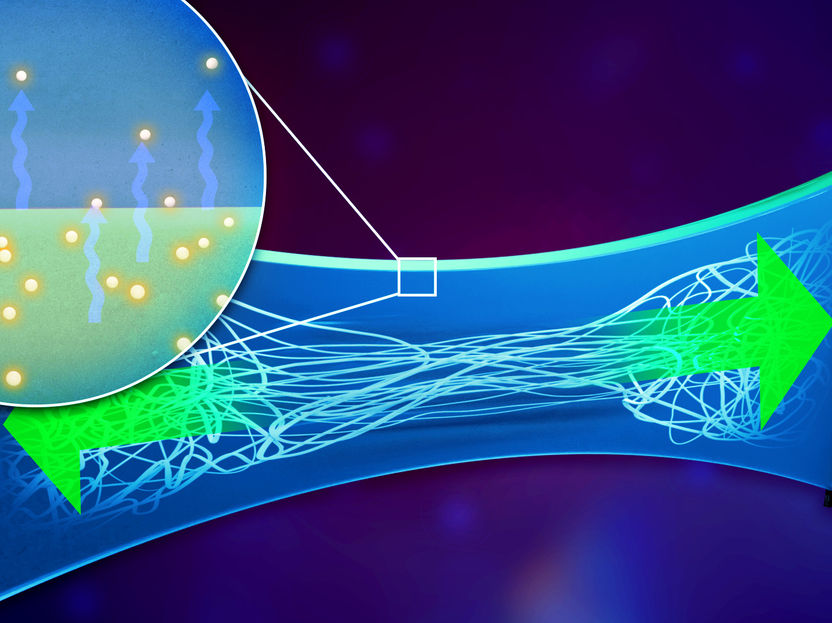
Stretchable Electronics: Conductive Polymer Optimized for Wearable Biosensors - A deformable patch that measures the heart rate or detects biomarkers in the sweat and feels as soft and flexible as one's own skin
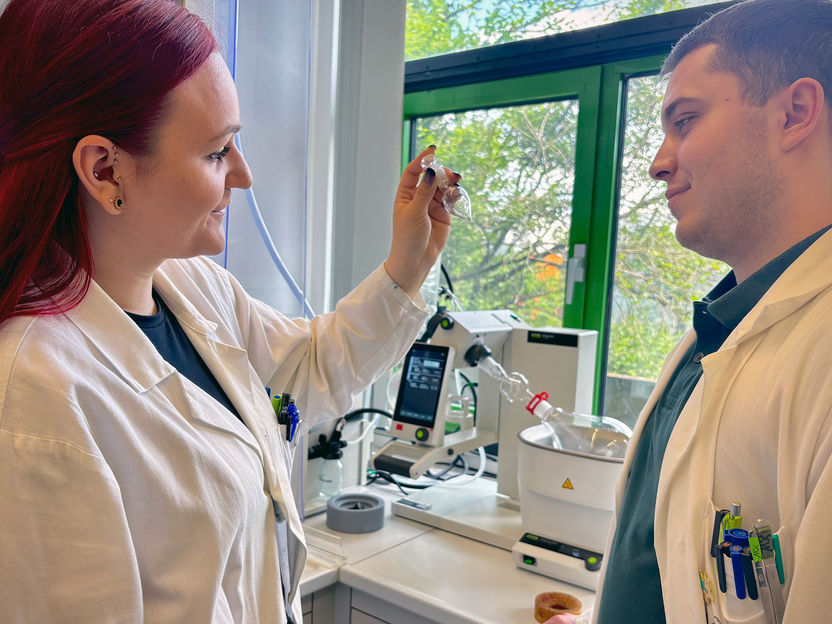
Producing Desired Epoxides from Pollutants - A new selective biocatalyst
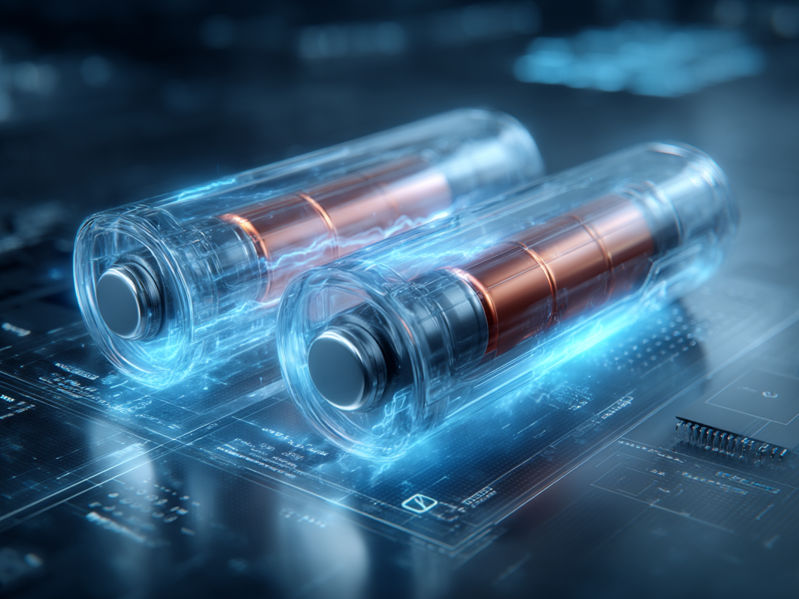
Progress towards potassium-ion batteries - Alternative battery technologies are vital for the green transition
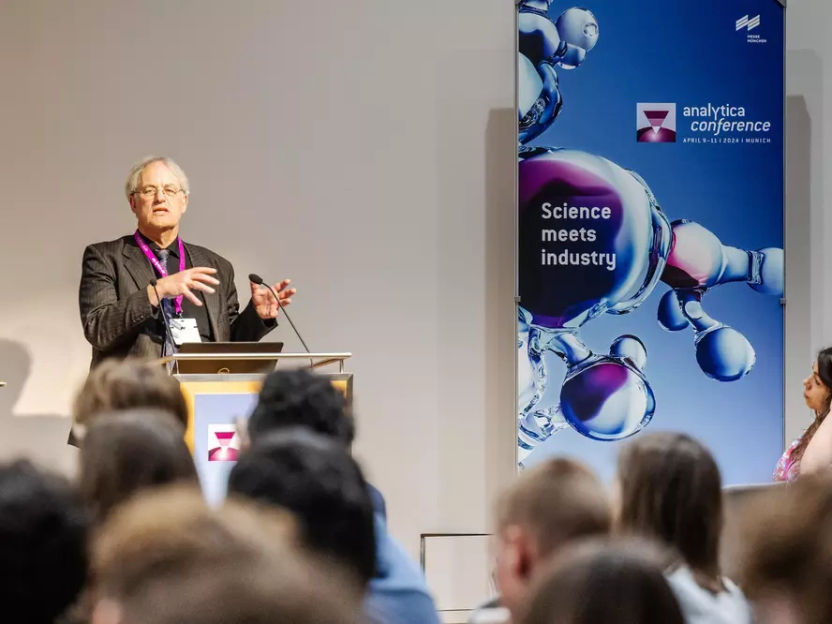
Analytica USA: Expert knowledge for research and practice - Special show Digital Transformation: a hands-on Smart Lab
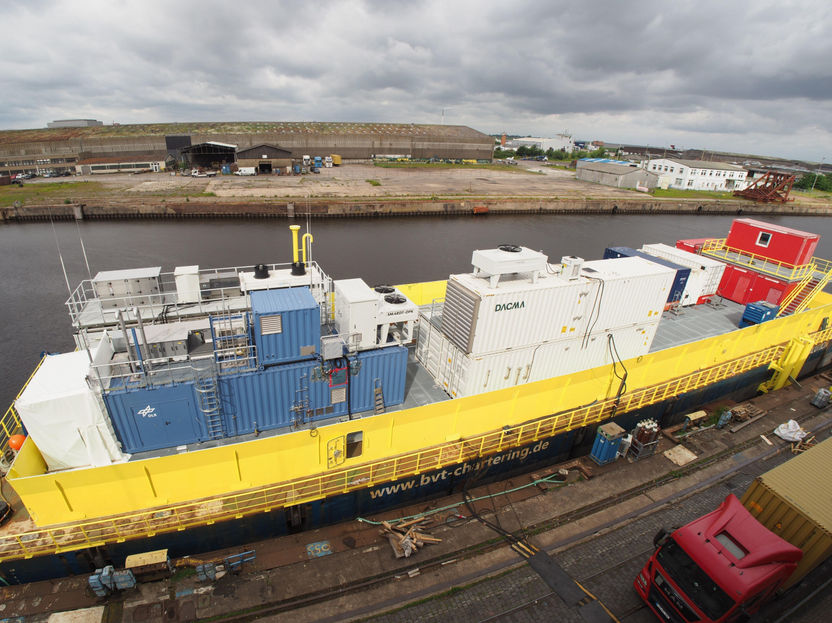
Synthetic fuel from the offshore wind farm - The first offshore facility for synthetic fuel production was inaugurated as part of the H2Mare hydrogen flagship project of the Federal Government
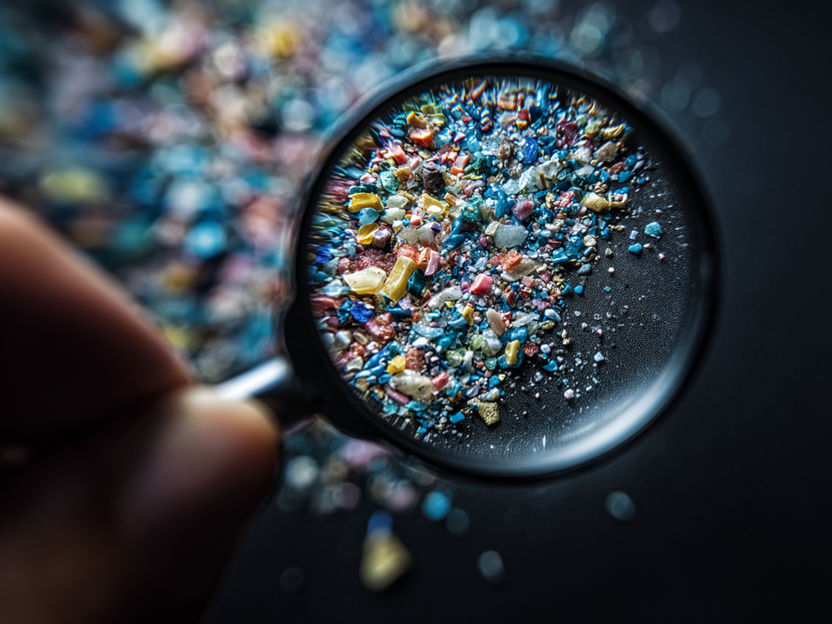
Identifying chemicals of concern in plastics – and pathways towards safer polymers - New study on chemicals in plastics published in Nature
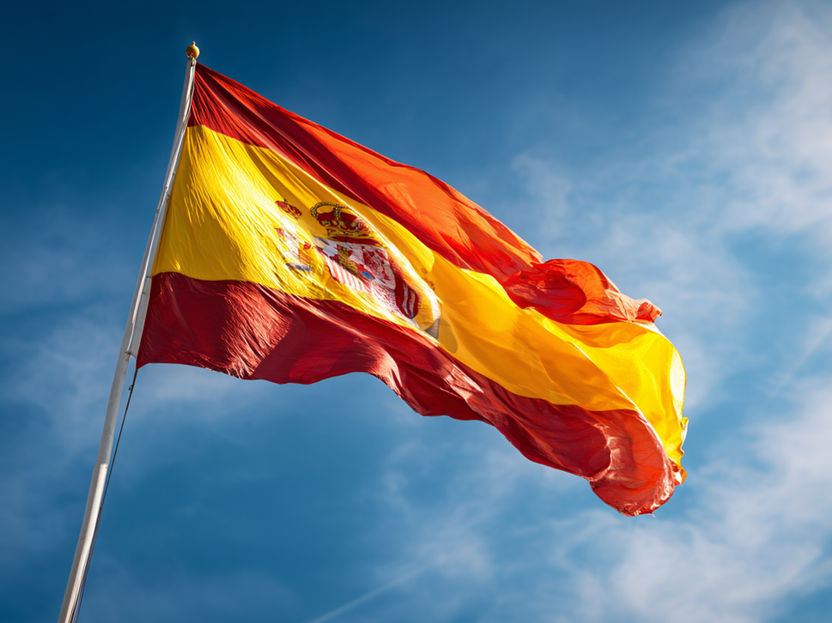